Order Batching: Automatic and Manual
This guide will cover manual and auto-batching in the Hopstack platform.
Manual batching offers precise control over order grouping and assignment, while auto-batching streamlines the process by letting the system intelligently batch unprocessed orders.
Only UNPROCESSED orders can be batched. For any orders in the EXCEPTION status, please resolve the exception reason before trying to batch them.
Manual Order Batching: Discover a comprehensive manual on optimizing order processing through manual batching in the Order Management system:
Selecting Unprocessed Orders: Access the Order Management interface and choose the orders you wish to batch. Ensure these orders are in the "UNPROCESSED" status for batching eligibility.
Selecting Unprocessed Orders
Commence Manual Batching: After selecting your preferred orders, proceed by clicking the "Create Manual Batch" button situated in the platform's upper-right corner.
Order Preview: Once the orders have been selected, as a user, you will be able to have a preview of all the orders, be able to sequence the order based on how you would like to priotize how the inventory will be allocated to each order.
On viewing all the orders on the preview, the user will be able to click Order ID to view the order Details including the available stock for order line items
As a user, you will be able to remove an order from batching, and doing so, the inventory allocation will be automatically updated to the current orders that are in Preview for the batching
As a user, if you have preference to certain orders, you will be able to change the sequence of the order, and based on that the order will be batched.
Note: If a product is included in multiple orders, the inventory allocation will follow the sequence you’ve selected. For example, if only 100 units are available and they are allocated to the first orders in the sequence, any remaining orders in the batch containing the same product may not be fulfilled due to insufficient stock.
Review Batch Details: Gain insights into fulfillable and unfulfillable orders, alongside the option to view splits for partially fulfillable ones ( a gated feature, pls contact your account manager to enable the Partial Fulfilment Feature). Explore comprehensive order breakdowns for enhanced transparency and informed decision-making. Access the detailed guide on Partial Fulfillment for further understanding, here.
Orders lacking sufficient quantity will not be batched, and will remain in the UNPROCESSED Status
Review Batch Details
Orders in Exception Status: If an order has a particular product or SKU is missing, those specific orders will move into the Exceptions.
When a batch is being created, a user will be able to review the orders that will move into Exceptions, as shown below.
If the user proceeds with batch by either clicking “Next” if there are fulfillable orders or “Cancel” if there are unfulfillable orders, and for those orders with missing SKU will move into exception. The user will see the confirmation message.
Assigning the Batch: Upon clicking "Create Manual Batch," you'll have the choice to allocate the batch to a designated packing station or picker.
Select Picker: Direct the batch to a specific associate in the warehouse.
Select Packing Station: Designate the order for processing at a particular packing station post-picking.
Should you opt for system-driven assignment, leave the options unchanged.
Complete Batch: Confirm by clicking "OK". The status of chosen orders will transition from "unprocessed" to "batched", signifying successful inclusion in the batch.
To quickly select all unprocessed orders for manual batching, use the status filter to choose "UNPROCESSED" and check the boxes for all orders.
Auto-Batching of Orders: Please find the steps below
Initiate Auto-Batching: Simply click the "Run Auto-Batching" button situated in the platform's top right corner.
Confirmation Prompt: After clicking the button, a prompt will appear asking you to confirm your selection.
Confirm Auto-Batching: Upon confirmation, all remaining unprocessed orders will be automatically converted into batches intelligently based on
Location in the warehouse
Type of products
Proximity to different products
SKU quantities in available UNPROCESSED orders.
Batch Availability: Once auto-batched, these orders will be made available to any picker on a first-come, first-served basis. This can be adjusted through the operations screen (please refer to this guide)
Please Note : You can track the user who batched the order by going to Audit Trail of the Order.
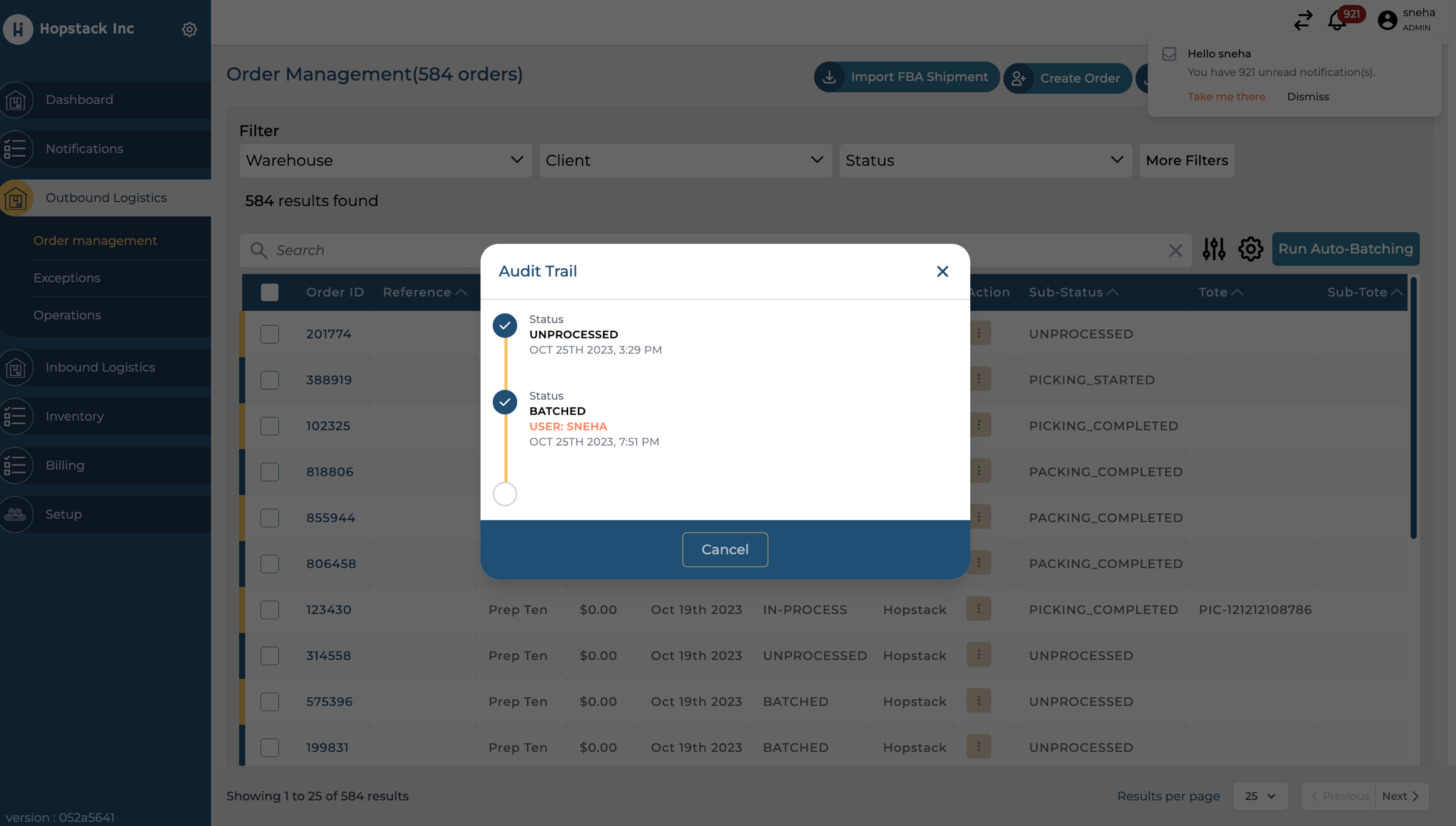
Note: Orders lacking sufficient quantity will not be batched and will remain in the Unprocessed status. They will no longer transition to the exceptions queue as previously observed.
Please ensure awareness of this behavioral change to optimize order management processes accordingly.
We hope this guide assists you in effectively batching orders on the Hopstack platform. If you have further questions or need assistance, please reach out to our support team.