Understanding and Managing Drop-shipping a.k.a. Cross Docking
Understanding Dropshipping (or Cross Docking)
Cross-docking is a practice in logistics of unloading materials from an incoming order and loading these materials directly to fulfil an outbound order, with little or no storage in between. This may be done to change the type of conveyance, to sort material intended for different destinations, or in our case, to perform prepping before sending it to Amazon fulfillment centers for FBA fulfillment.
Within the Hopstack warehouse management software (WMS), cross-docking is leveraged to facilitate seamless order fulfilment operations, particularly for dropshipping. The term 'dropship' is used to indicate a process that bypasses the traditional warehouse storage and picking stages, accelerating the supply chain by reducing or eliminating the need for material handling and focusing solely on value-added services like prepping.
Standard Fulfilment Process vs. Dropshipping Process
The standard fulfilment process, as utilized in traditional warehouse operations, typically includes the following steps:
Receiving: The goods arrive at the warehouse.
Putaway: The received items are placed into storage within the warehouse.
Storage: Goods are stored until an order is placed.
Picking: Items are collected from their storage location in response to an order.
Prepping: The picked items are prepared for shipment.
Packing: The prepared items are securely packaged.
Shipping: The packaged goods are shipped to the customer.
The dropshipping process within the Hopstack WMS, however, significantly streamlines these steps:
Receiving: The goods arrive at the warehouse, similar to the standard process.
System Automatic Putaway: Hopstack automatically puts the received goods into a virtual location, bypassing physical storage.
System Shipment Creation: Hopstack creates a shipment on the designated platform (e.g., Amazon).
System Automatic Picking: The system virtually "picks" the order from the virtual location and places it at the prepping station.
Prepping: The order is prepared for shipment, just like in the standard process.
Packing: The prepared items are securely packaged.
Shipping: The packaged goods are shipped directly to the customer.
With drop shipping, the user workflow is simplified to just:

The Hopstack platform supports two types of dropshipping (or cross-docking) orders:
FBA Dropship - In this case, the items received in a consignment are used to create a shipment plan on Amazon automatically. This shipment plan is made to send items to an Amazon fulfillment center.
Regular - In this case, the items received in a consignment are used to fulfill an order. This order may be from any non-Amazon order source i.e. Shopify, eBay, or even manually created on Amazon.
Steps to create drop-ship consignment:
Step 1: Go to the consignments screen in the inbound logistics module, click on Add consignment and choose Dropship.
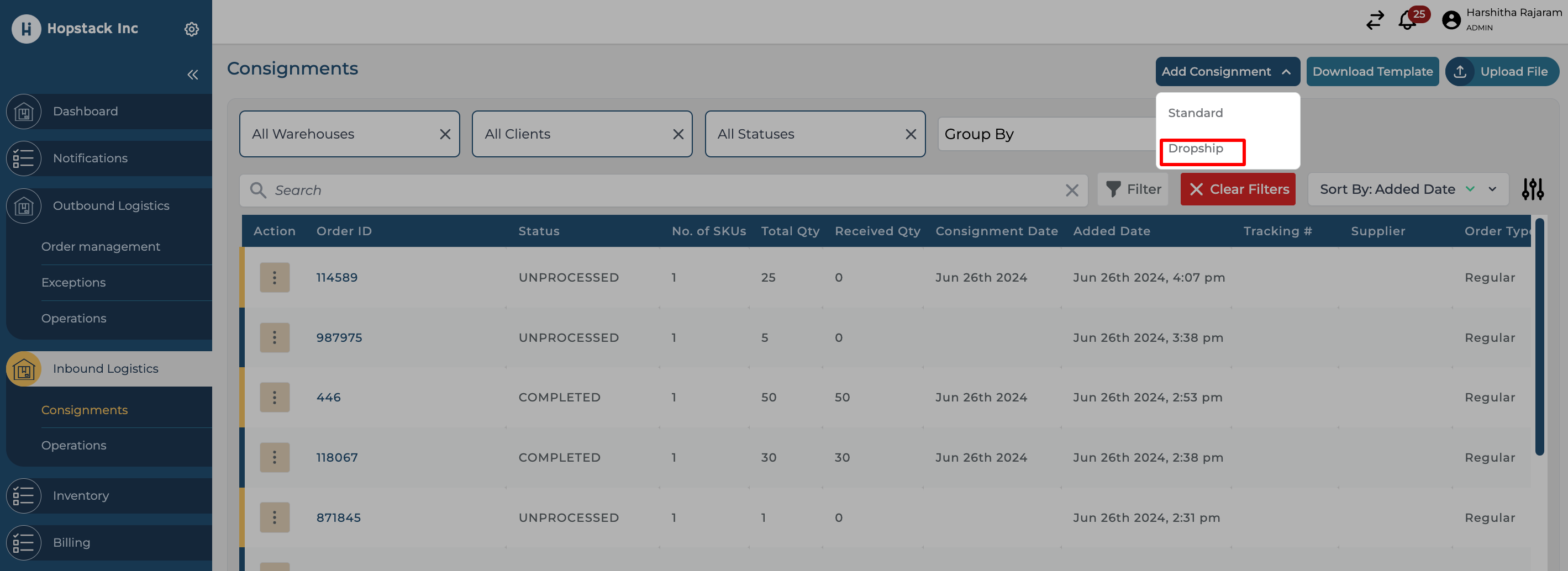
Step 2: Select Warehouse and Client in the Basic info screen and click on Next.
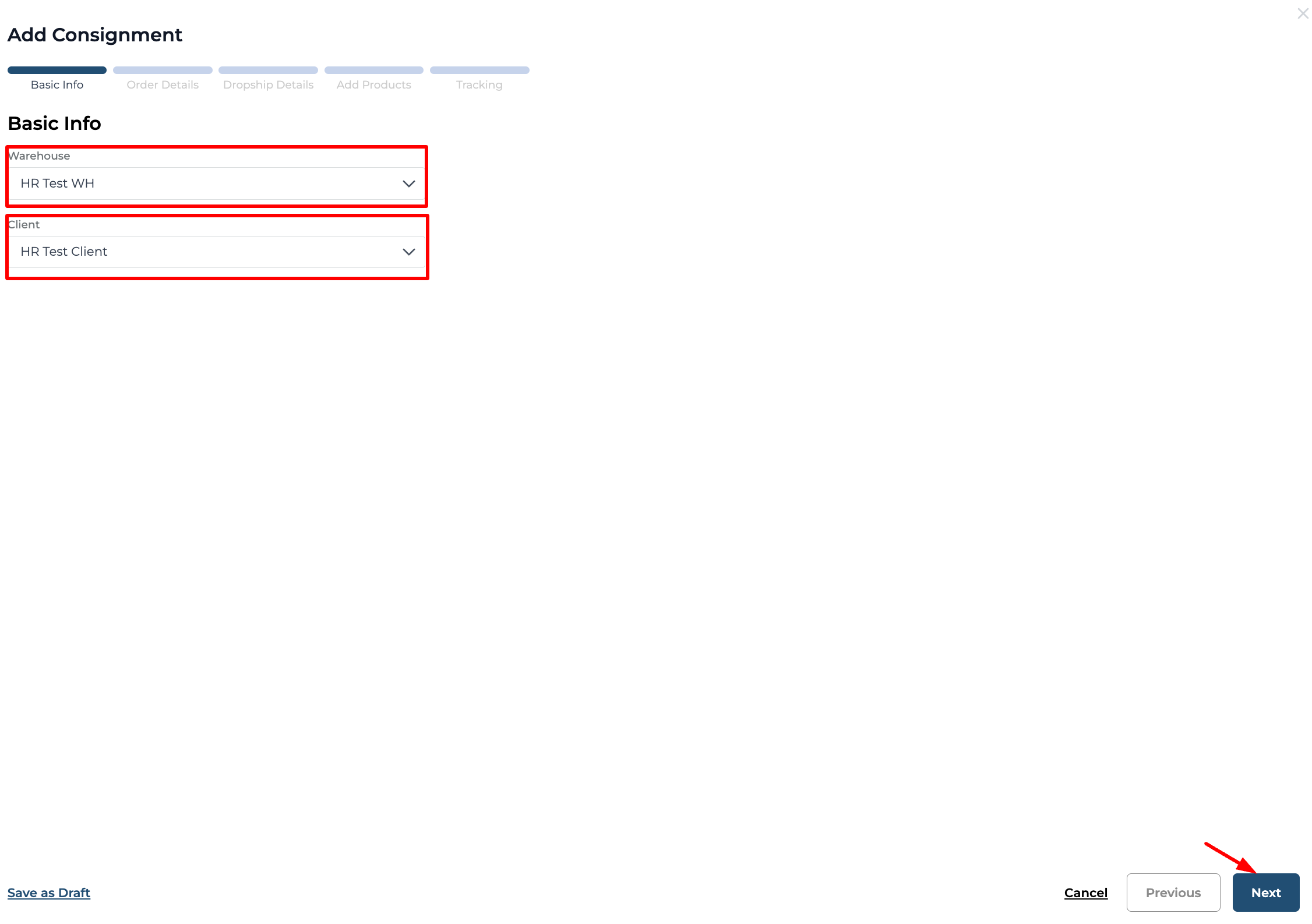
Step 3: In the order details screen, fill in the order details and click on Next.
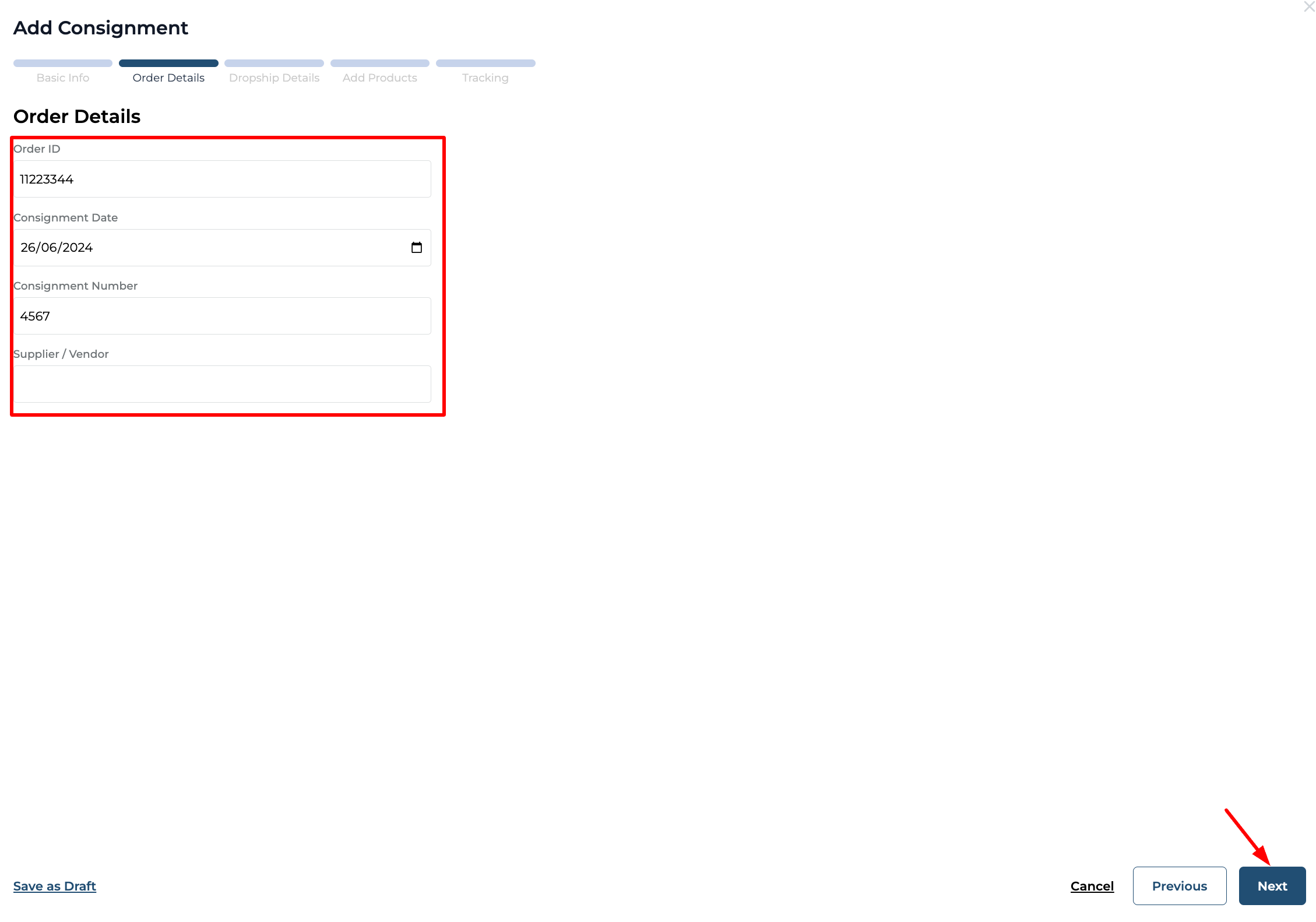
Step 4: In the Dropship details screen, choose the dropship type.
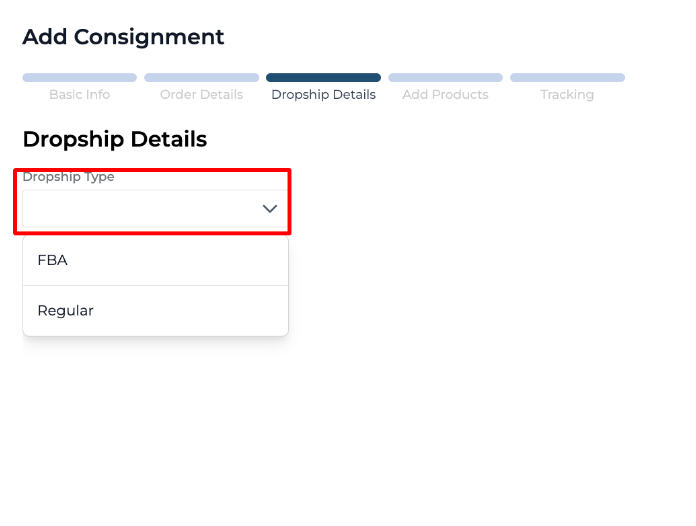
For demonstration purposes, Regular is selected. The users are able to choose an option for shipment label where the label could be from Public URL, System generated or they can upload file. Click on Next.
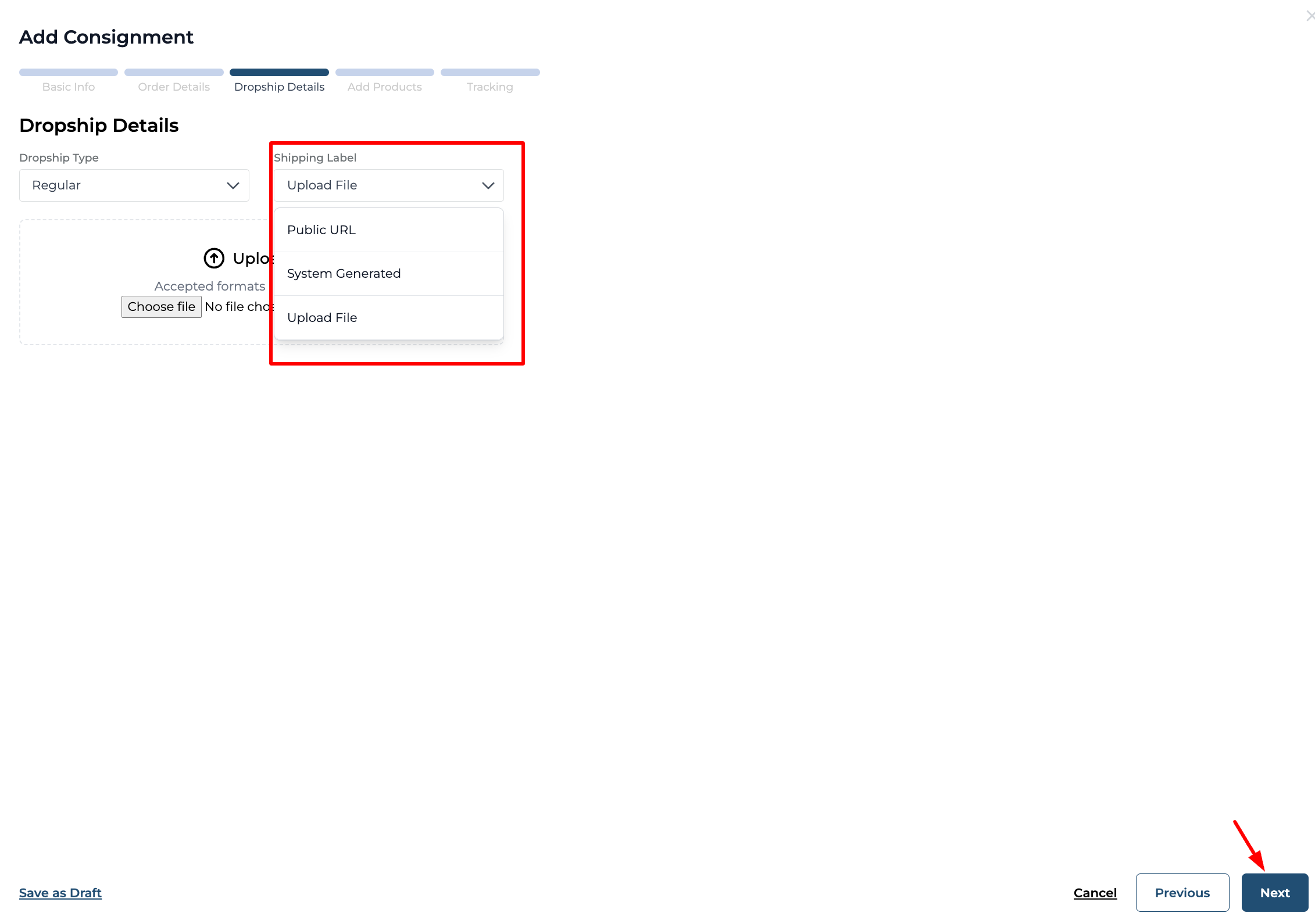
Step 5: In the add products screen, the users can search for the products they would like to add and click on select. Then enter the product details. Users can select on “+Add More” to add more products to the consignment. After completing adding products and filling in product details, click on Next.
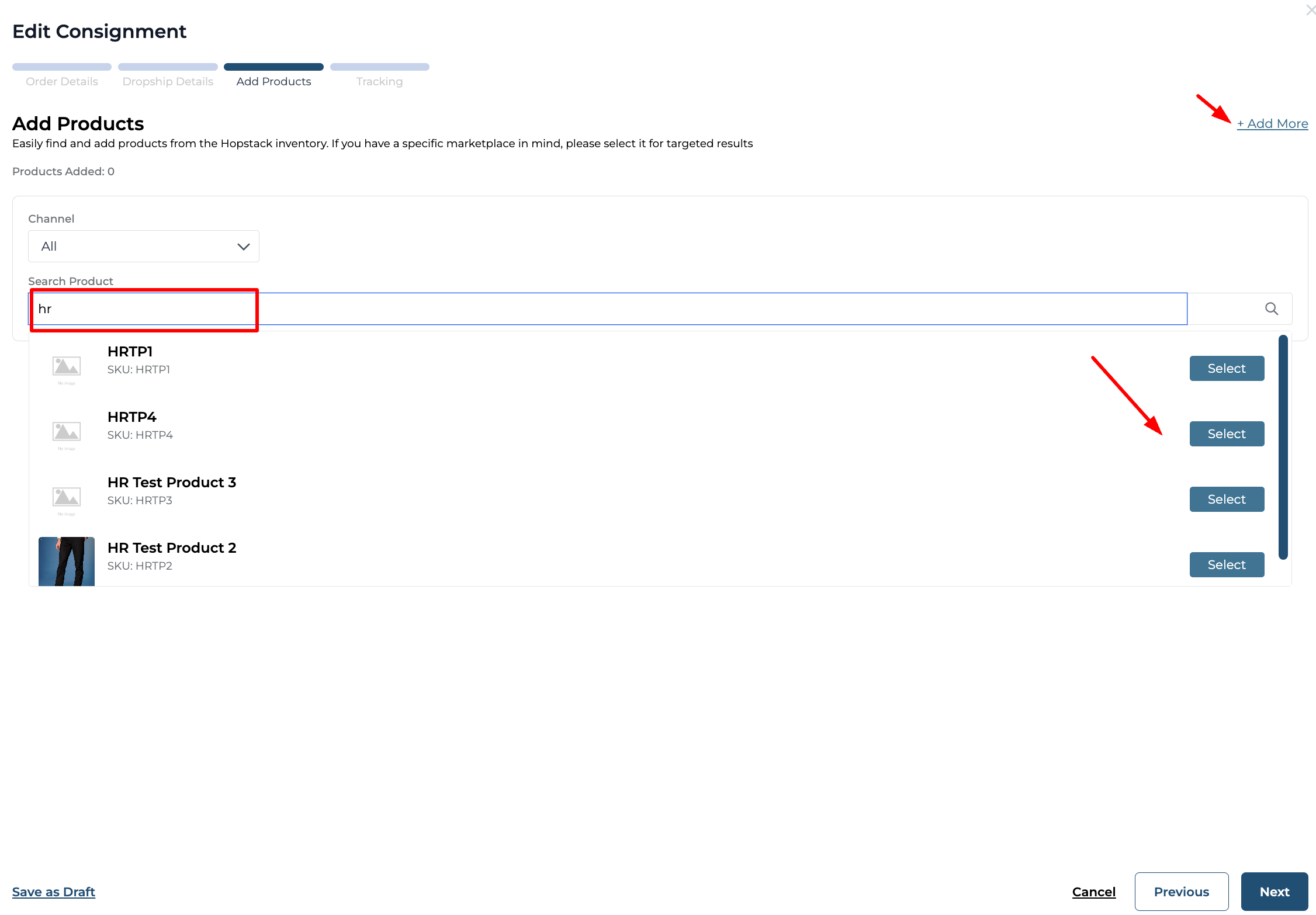
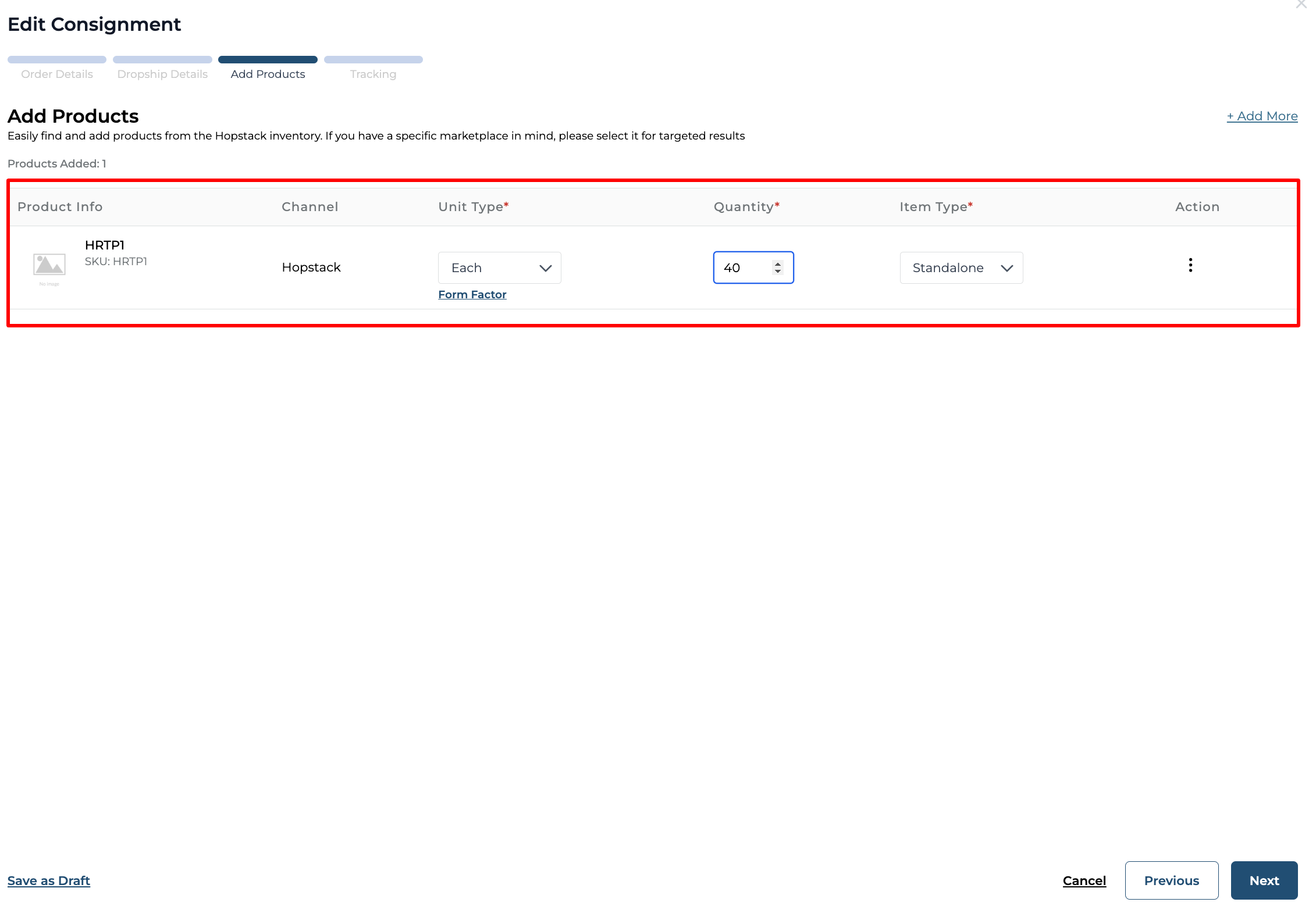
Step 6: Users have the option to add tracking information in the tracking screen. Click on create to complete creating the shipment.
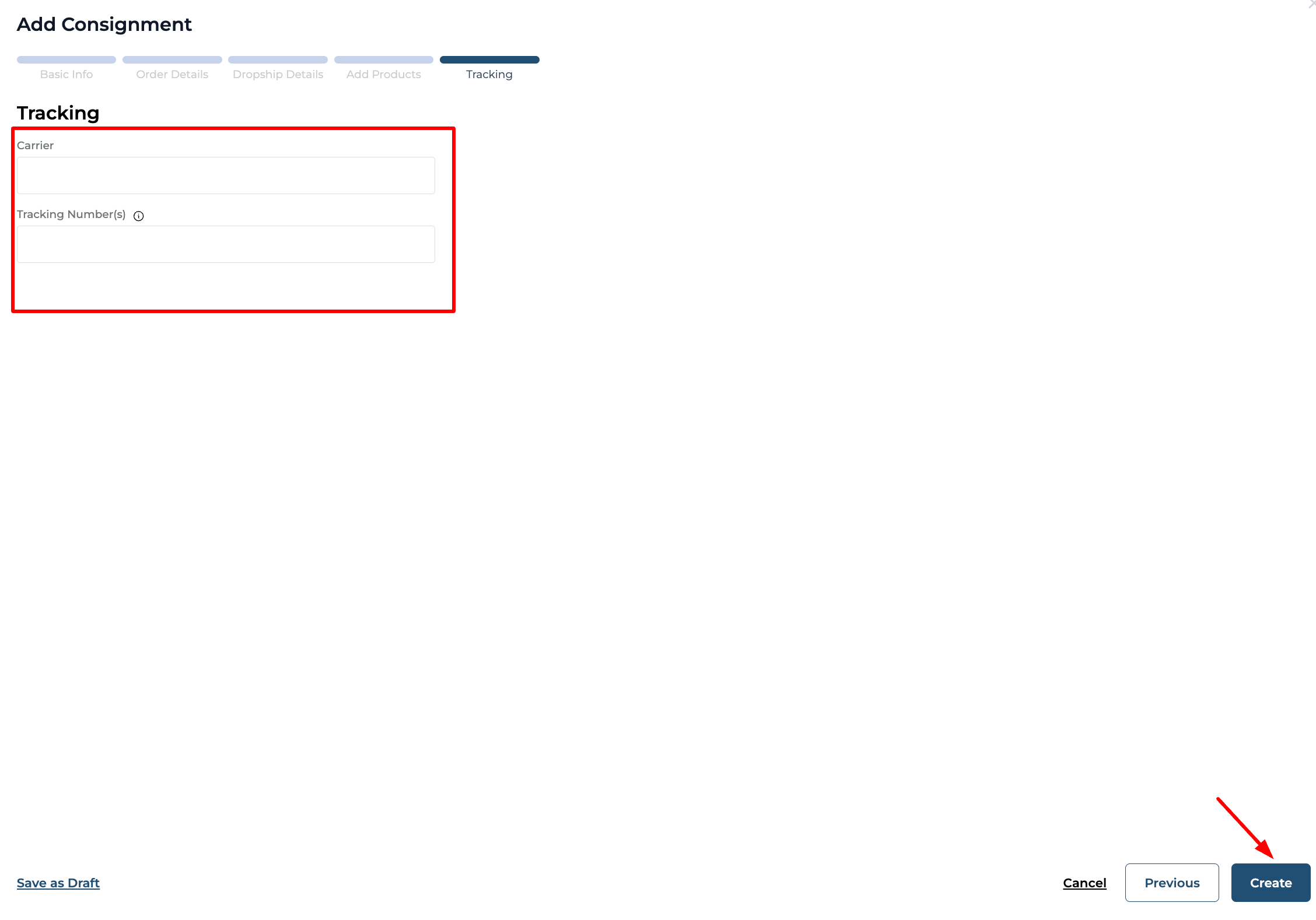
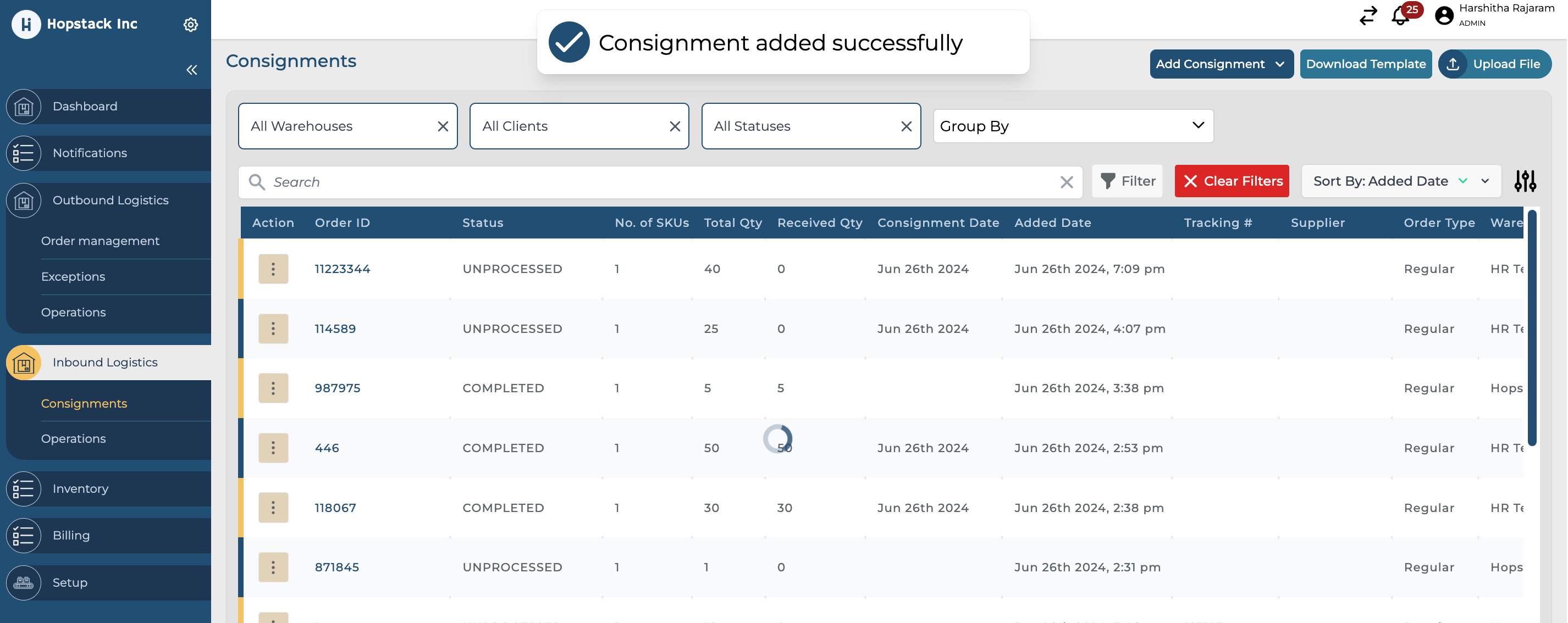
(Note: During the process of creating the consignment user has the option to save as draft and resume creating the shipment by using the edit action.)
Steps to receive the consignment.
Step 1: Enter the associate receiving screen.
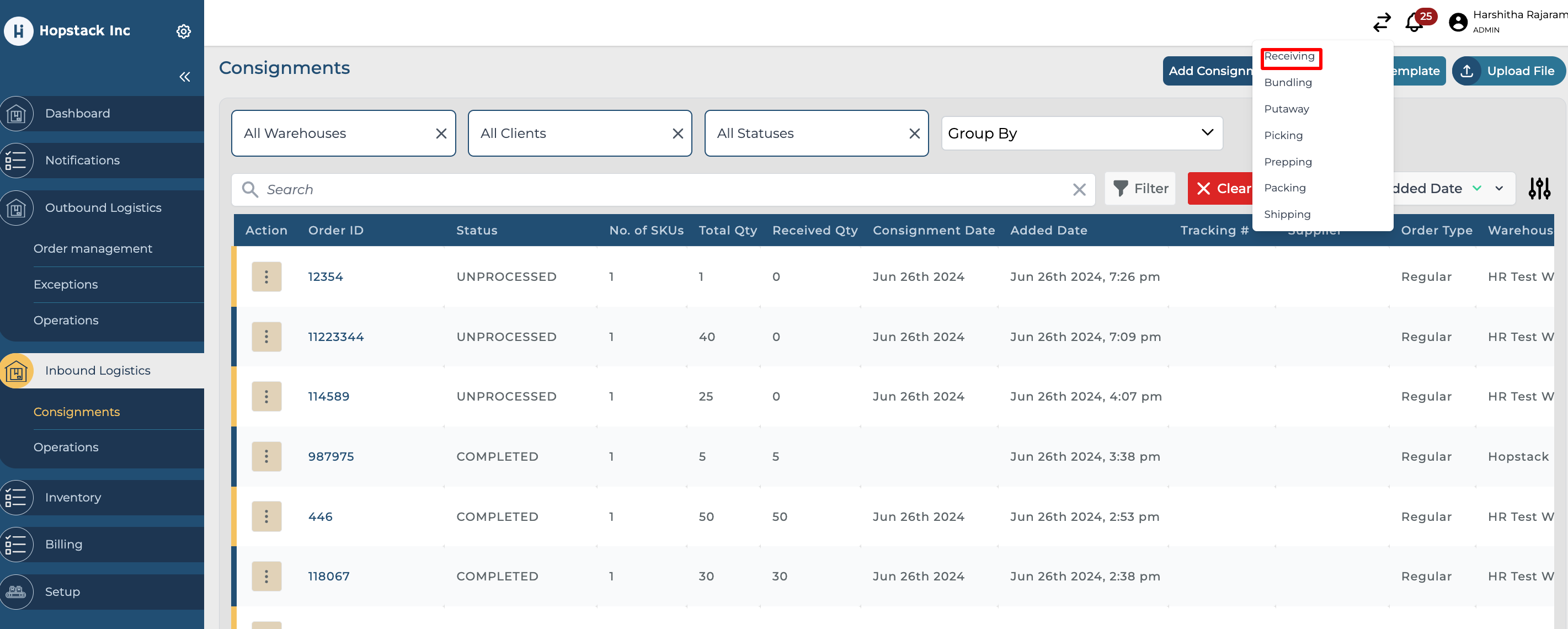
Step 2: Select Client.
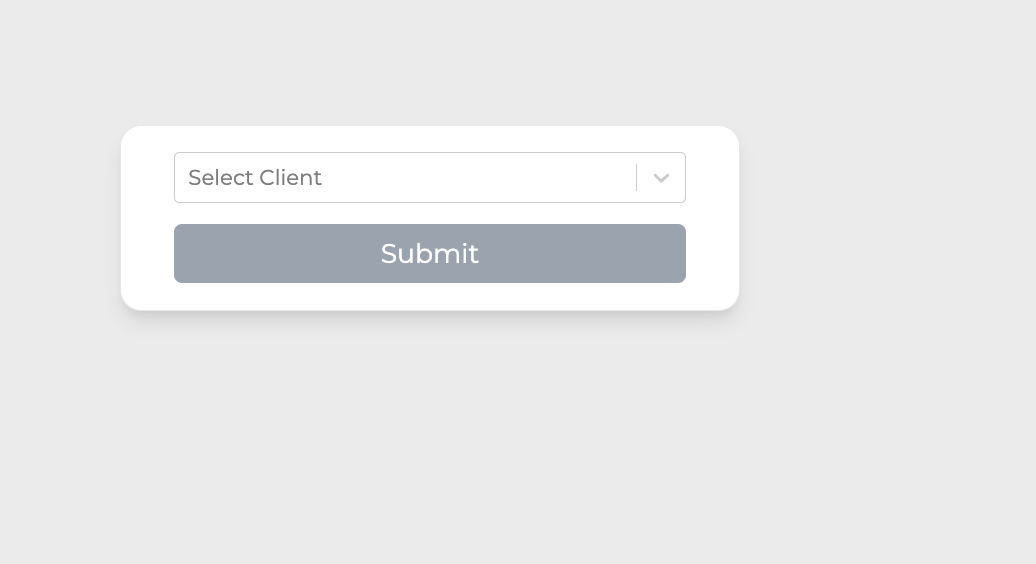
Step 3: Select the consignment order from the list view or enter the tracking number in the detailed view.
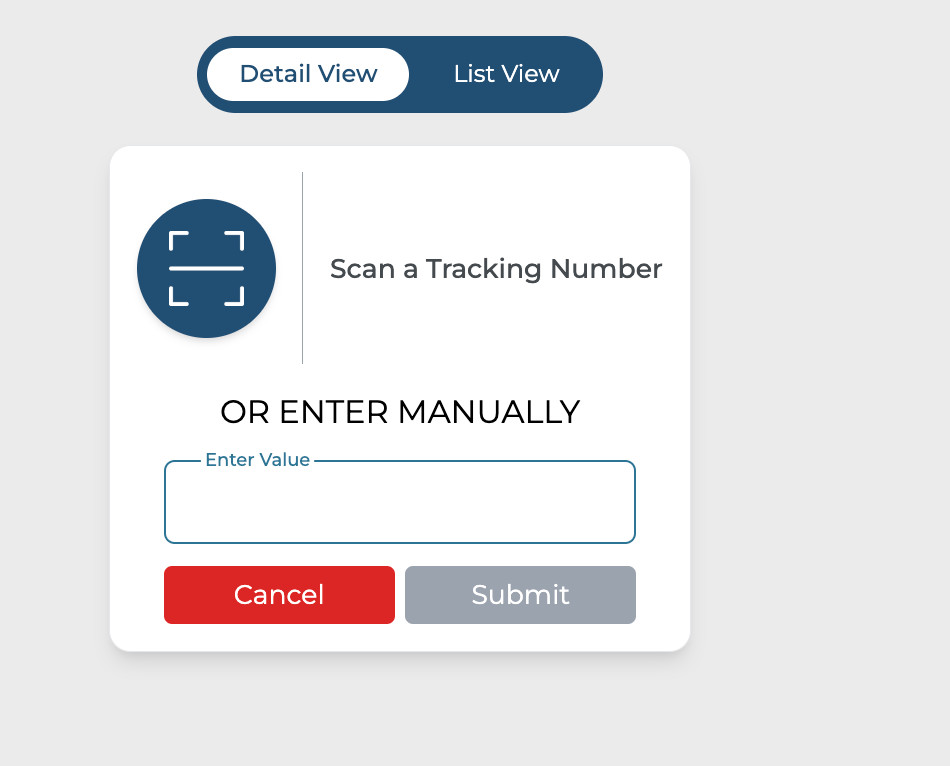
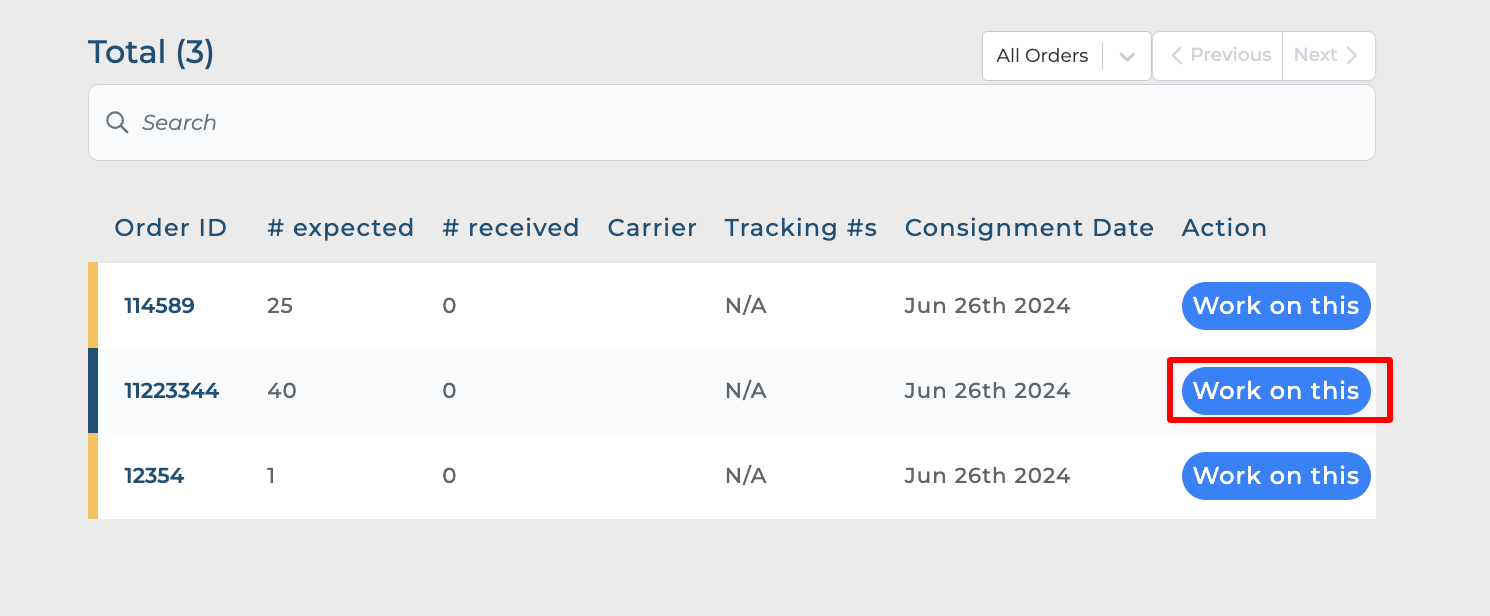
Step 4: Scan the item code
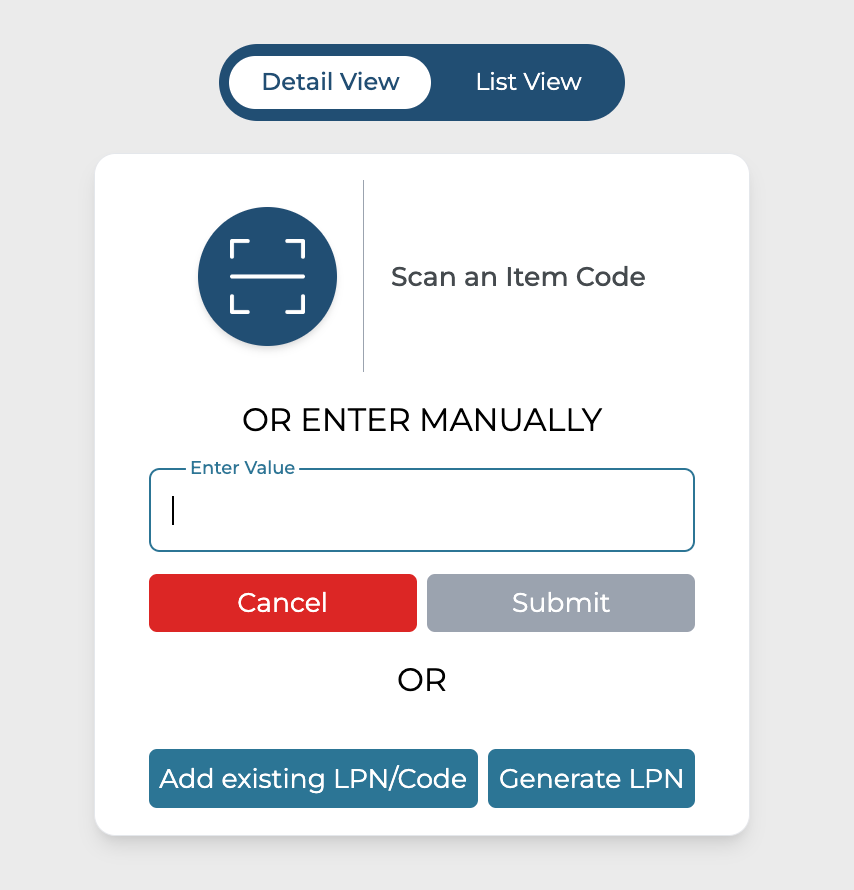
Step 5: Verify product details, select virtual dropship location and hit confirm to complete receiving the items.
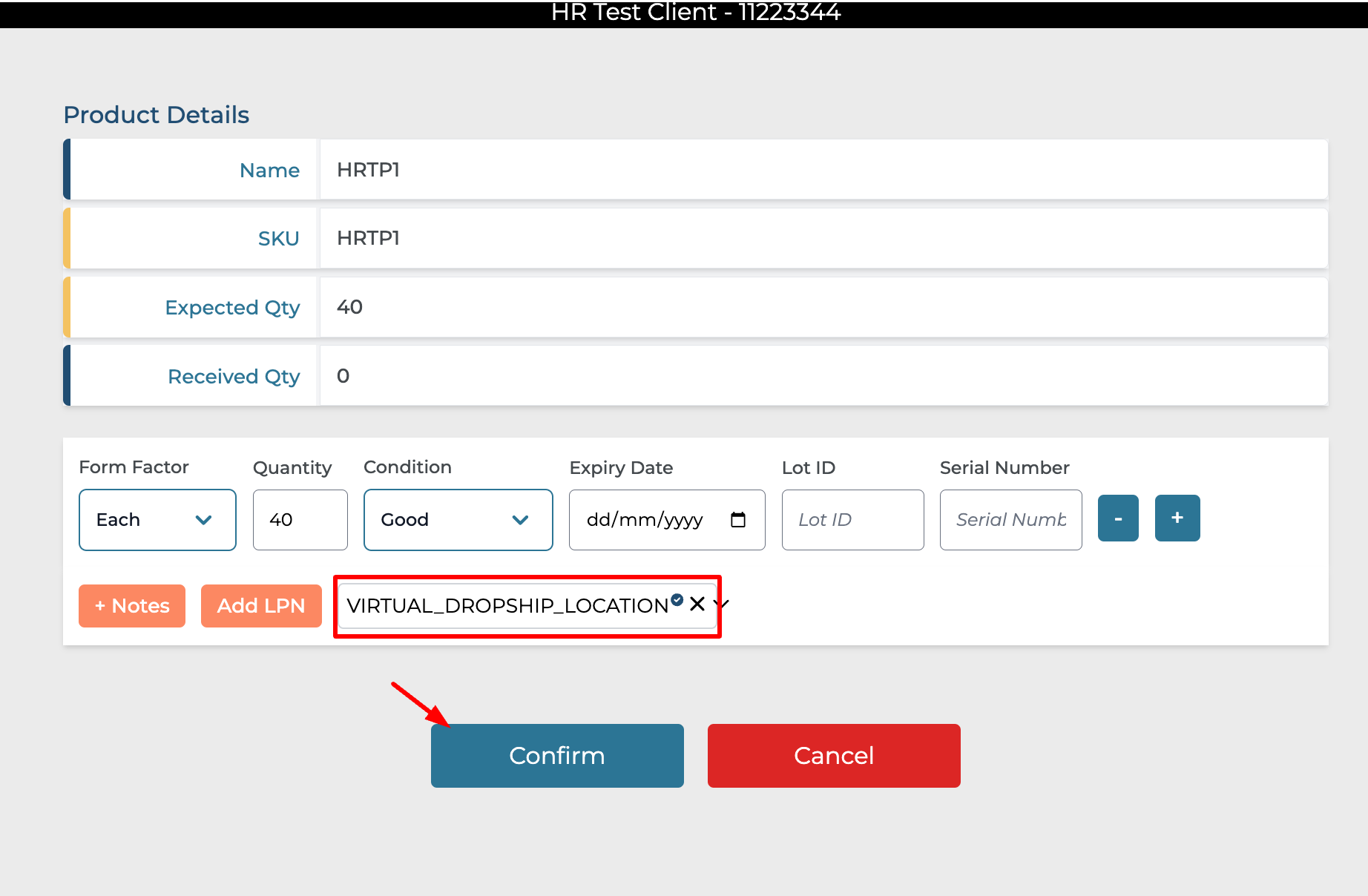
Once the consignment is received, system automated picking and shipment creation occurs. The shipment created will be visible in the order management screen in the outbound Logistics module as shown below.
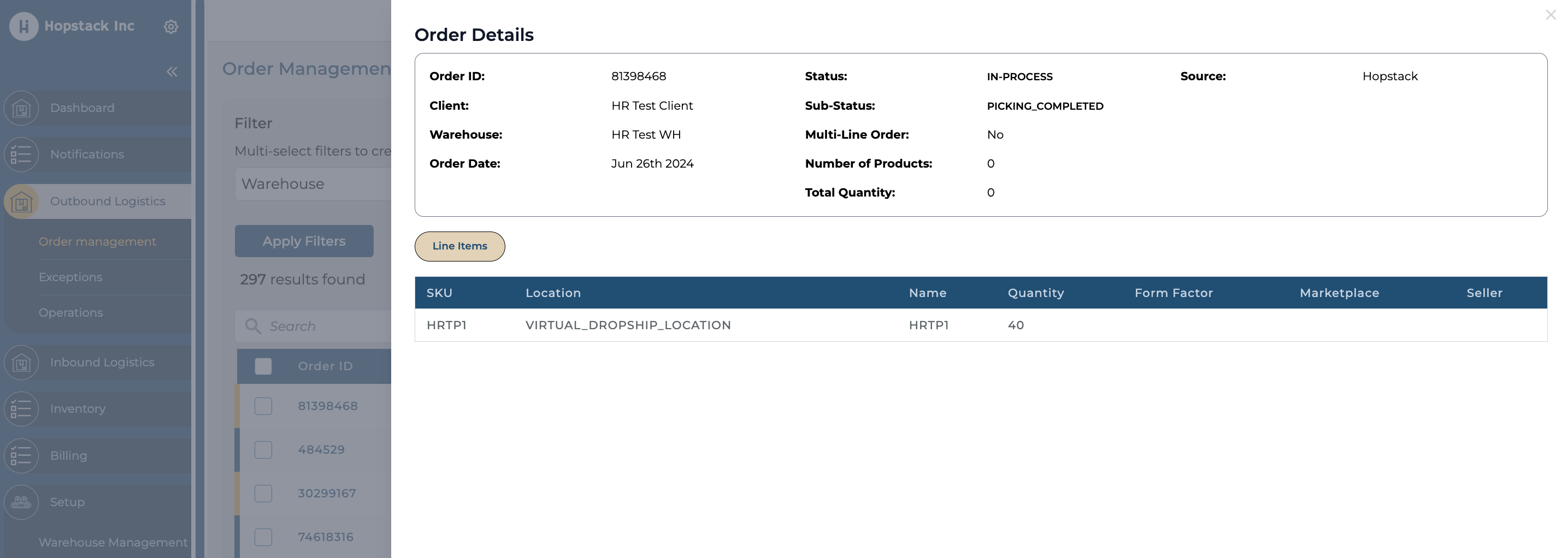
The drop-ship order is also visible in the associate view for both prepping and packing.
Drop ship order in the prepping screen:
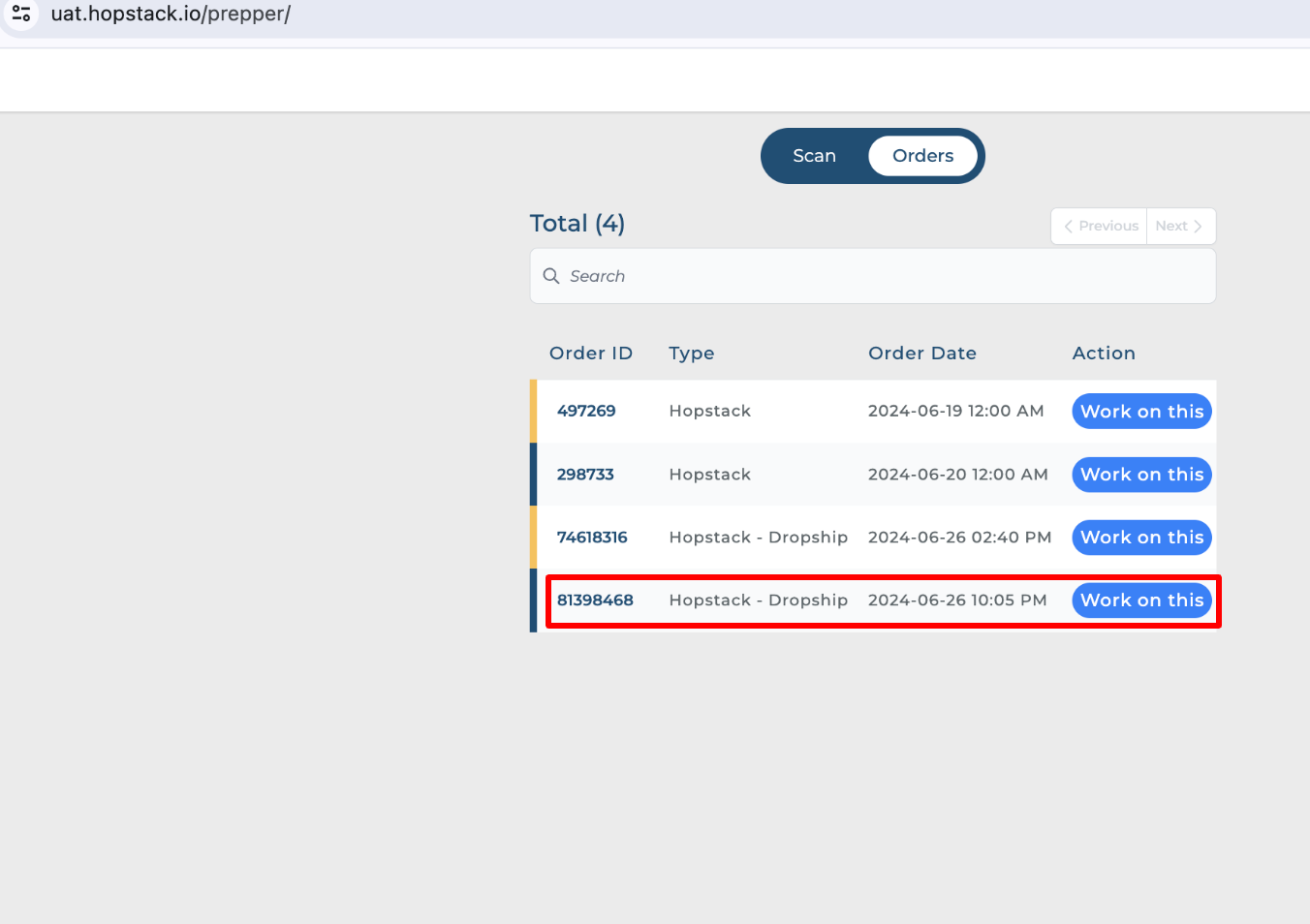
Drop ship order in packing screen:
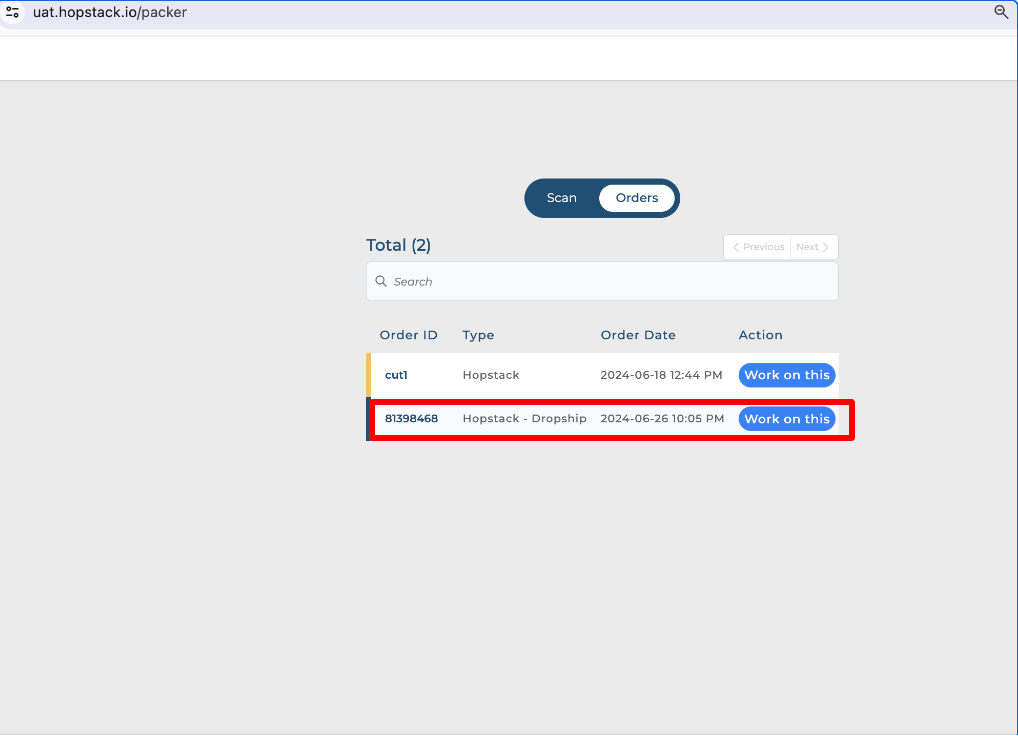
Users will be able to perform the outbound workflow ie. packing → shipping or prepping → packing → shipping for the consignment like any other order.
Note: Even though Hopstack performs some steps automatically, it's crucial to manually complete and verify steps like prepping, packing, and shipping to ensure accurate and efficient order fulfilment.
For more assistance with setting up or managing dropshipping within Hopstack, please refer to our other Help Center articles, and tutorials, or contact our support team directly.