Assign Warehouse for Multi-Warehouse Operations
This guide provides instructions on managing order fulfillment when associated with a specific warehouse. This system is designed to ensure that orders are fulfilled efficiently by checking stock levels at their associated warehouses.
Each order, upon its creation, is associated with a specific warehouse. When the fulfillment process initiates:
The system checks inventory only at the designated warehouse.
If the designated warehouse doesn't have the full quantity required:
The order will be flagged and moved to an "exception" status.
This mechanism helps in identifying potential fulfillment issues and offers a quick solution by indicating an alternate warehouse with the required stock.
Viewing Exception Reasons
To understand the specific reason for any order exception:
Navigate to the Exceptions screen on the dashboard.
Look for the order in question, which should be highlighted due to its exception status.
To the right of the order details, you'll find the Action column.
Click on the button labeled Check Reason.
A popup or a new screen will appear detailing the exact reason for the exception.
This feature ensures transparency in the order fulfillment process and allows users to quickly identify and resolve issues.
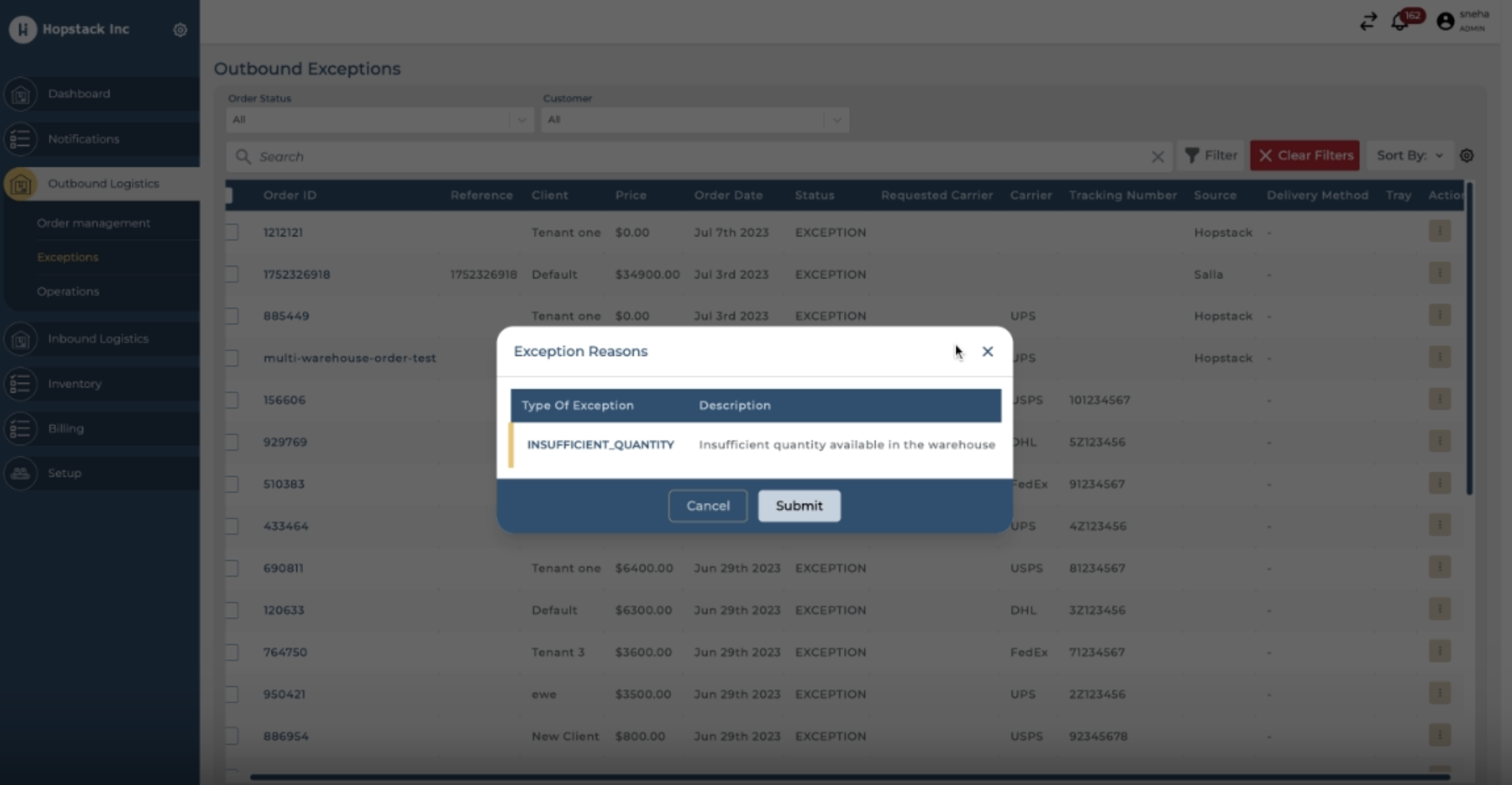
If it says insufficient quantity in the warehouse. And if there is another warehouse that can fulfill the same this can be changed after doing the following steps:
Reassigning an Order to a Different Warehouse
If an order is in an exception due to inventory mismatch and you'd like to reassign it to a different warehouse:
On the Exceptions screen, locate the specific order.
Under the Action column, click on the button labeled Assign Warehouse.
A dropdown menu or a new screen will appear displaying the list of available warehouses.
Choose the warehouse that has the required stock.
Confirm the change. The system will update the order's associated warehouse.
Once reassigned, the order can then be processed and fulfilled from the new warehouse, ensuring that there are no unnecessary delays in delivery to the end customer.
Note: It's essential to regularly check the exceptions screen, especially during high order volume periods, to ensure timely fulfillment and high customer satisfaction.